Printing Quotation Request Tips
Printing is a highly detailed process in which every component impacts the end result, as well as the cost. Therefore, it is critical to provide vendors with specifications that are as accurate and complete as possible.
This guide outlines the information that should be included in any printing quotation request, regardless of the size or scope of the project.
Contact Information
Include the name, email address, and phone number of the primary contact person for the project. Make note of the preferred method of contact to ensure timely communications.
Timeline
Provide the vendor with dates for both artwork submission and final delivery. Be clear if the project is tied to an event. It is good practice to designate that delivery take place by noon, or another time of day, so that there are no emergencies.
Artwork
If you have samples of the artwork, go ahead and include with the quote request. This is always helpful, and usually clarifies many questions the printer would have. If the artwork is not ready, then try to give the vendor information such as:
- Software used (Quark, InDesign, PDF) and version, if applicable.
- File submission method (CD, FTP site, etc.)
- Date to expect artwork receipt.
You may also specify that the vendor’s price include the cost of two rounds of proofs, as well as a given number of working days to output them.
Lastly, ask the vendor for prices on additional artwork alterations, which would be added to the cost of the initial quote, if requested.
Order Description
This information must be clear to the vendor. Otherwise, quotes may be inaccurate, or worse, result in additional costs and delays once the project is in production. The best way to ensure accuracy is to provide a mockup and/or PDF of the artwork to the vendor at the time of the quotation request.
Quantity: How many total pieces are being ordered? Avoid using Roman numerals, abbreviations, or terms such as “reams,” “boxes,” or “pallets.” Use the total number of individual printed pieces that you desire.
Number of pages: Remember, the front and back of one page is equivalent to two (2) pages.
- Self cover: If the document has multiple pages, and all of them are printed on the same type and weight of paper, then it is called a “self-cover.”
- Plus cover: If the document has multiple pages, and the outside cover is printed on a different kind of paper than the interior pages, then it is called a “plus cover.”
- Remember, it is not possible for a booklet to have an odd number of pages. Make sure that the page count is correct.
- When printing page numbers, always use even numbers on the left-hand page, and odd numbers on the right-hand page.
Size: This is one of the most often overlooked and mistaken details. Other than quantity, no other component impacts the vendor's planning of a job than size.
Specifications must include both the flat size and finished size of the project.
- Flat size: This refers to the size, measured in inches, of the document if it were to lay flat. For example, the flat size of a standard LSU notecard is 5.5” x 8.5”. When it is folded in half, the size changes.
- Finished size: This refers to the size, measured in inches, of the document once all printing and finishing is complete. That includes any cutting or folding. For example, the finished size of that same LSU notecard is 5.5”x 4.25,” which is half of its original flat size.
If unsure of the project’s dimensions, provide a printout at full scale, with crop marks, for the vendor to measure. Also, see this example for reference:
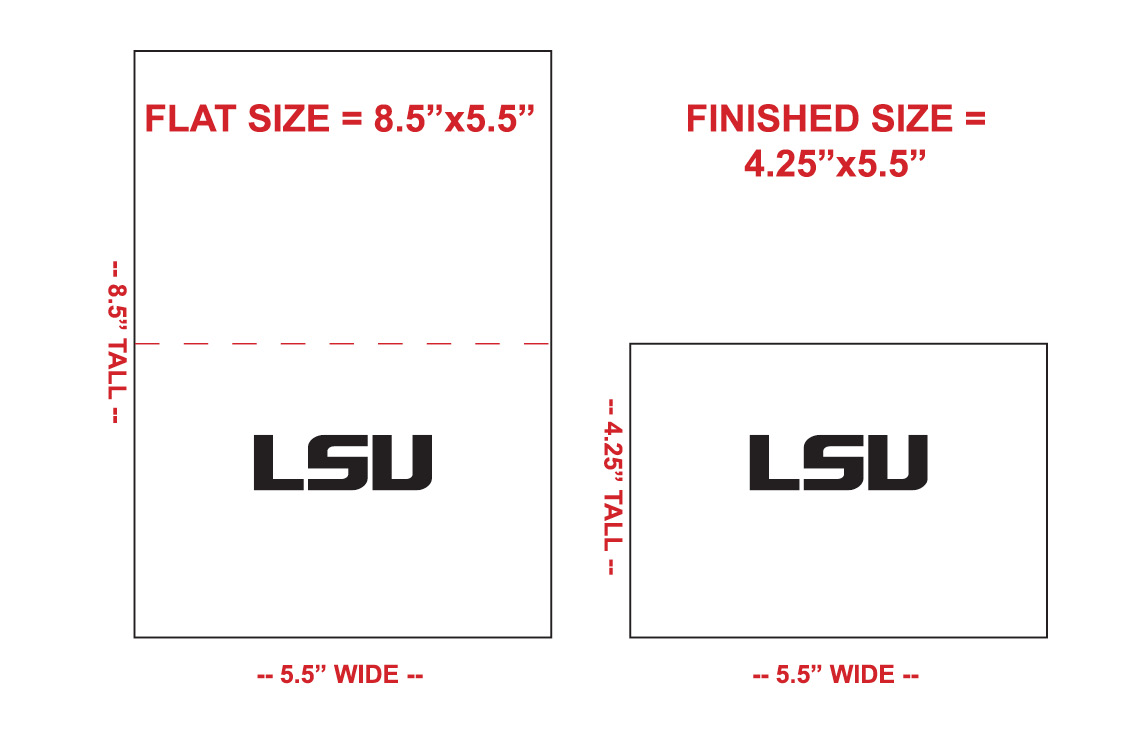
Bleed: Artwork that extends to the edge of a sheet or page after trimming is referred to as a bleed. Vendors sometimes add charges for bleeds, so relay this information in the quotation request.
Paper: There are endless differences in types of paper: recycled, linen, bright white, opaque, etc. To save time and money, ask the vendor to provide samples of paper that is regularly kept in stock. The biggest savings will come from paper that is available on state contract, which is subject to change every six months.
When creating a quotation request, include the type of paper desired. If possible, use the brand name (such as Lynx Opaque White). If unsure about the brand, give the following details:
- Color
- Weight: both cover and text weights are denoted in pounds (or a number followed by a “#”). The higher the number of pounds, the heavier and thicker the paper. For example, LSU business cards are printed on 80# cover weight paper, while envelopes are printed on 20# text weight paper
1. Cover: Use for pocket folders, postcards, and the outside covers of booklets
2. Text: Use for fliers, leaflets, and the interior pages of booklets and magazines.
- Finish: The choices here are also extensive, but boil down to two varieties:
1. Coated: These papers have a coating that allows the ink to sit on top of the paper. Most commercial magazines are printed on coated paper.
2. Uncoated: These papers have no coating, so that ink saturates the paper. Sometimes, the result is a darker color than may be desired. Uncoated papers also have a more notable texture than coated papers.
Inks and Color: Ink selection determines how the printed colors in a document are rendered, and has an impact on the total price. There are two different approaches to printing color: process printing and spot color printing.
- Process: Process printing layers inks on top of one another, which combine to produce additional colors. The most common type of process printing is four-color printing (also known as CMYK printing), in which four inks (Cyan, Magenta, Yellow and Black) are layered in varying degrees of density to render a full-color image.
- Spot: Spot color printing uses one or more Pantone inks. Usually the colors are not layered, but they can be combined to create the effect of an additional color. When printing the official LSU colors, always use Pantone 268 (purple) and Pantone 123 (gold). If using other spot colors, be sure to designate them in the specifications.
Please note, printers generally charge less for black ink than for any other spot color.
Also, if the document is intended to run through a desktop printer or copier at a later time, then ask the vendor to use laser ink. This will ensure that the ink on the printed piece does not smudge or deteriorate when run through another printer. Examples include certificates, labels, and nametags.
Finishing: Finishing refers to all the final touches on the document once the ink has dried. This includes scoring, folding, embossing, die cutting, and packaging. Let vendors know if finishing services are needed at the time of the quotation request.
- Scoring: If using a cover-weight paper, the document must be scored before it is folded in order to avoid uneven folds or creases in the paper.
- Folding: There are many different types of folds. The most common is the “A fold,” which folds a sheet at the center into half its original size. For example, LSU notecards use an A fold. Visit this link to learn more about folds.
- Die cutting: A die is used to cut out shapes into paper; the most common are for pocket folders. Many vendors have standard dies that can be used without additional charges; otherwise, additional time and cost will be involved.
- Perforation: Commonly used when a return mailer is included in a publication, perforation facilitates tearing the paper at a specific location.
- Packaging: Specify if the job needs to be shrinkwrapped, boxed, or otherwise packaged in a desired way.
- Other details include padding, hole punching, embossing, and many other options. Just be clear in the specifications to ensure the quote is accurate.
Binding: This refers to the way a multiple-page document is held together.
- Saddle stitch: This is one of the most economical ways to bind small documents of 72 pages or less. Saddle stitching involves stapling together folded sheets of paper on the fold itself. Most magazines, like Newsweek, are saddle-stitched.
- Perfect bind: Pages and cover are held together by a flexible adhesive which keeps its strength and resiliency for a long period of time. This is recommended for publications with 80 or more pages. Most paperback books are perfect bound.
- Plastic comb binding: Ideal for manuals and other documents that must lie flat when open. Accommodates several hundred pages.
- Coil binding: A better-looking alternative to plastic comb binding, this solution also allows the book to lie flat when open. A continuous, spring-shaped, crush-resistant spiral holds the book together. Plastic and wire options are available in many colors and styles.
Delivery Instructions: Many vendors may not be familiar with the LSU campus, so it is very important to give clear delivery instructions. First, the vendor should obtain the appropriate parking permits and Easy Streets gate wands from the Office of Parking & Transportation.
In the quotation request, include:
- Delivery address
- Delivery contact person (if different from project contact)
- Building access details (loading dock, lack of elevator, etc.)
Mailing: If the job is to be mailed, then let the vendor know who is responsible for mailing.
- Are you asking the vendor to give a price to sort, label, and mail the project? If so, the vendor must provide Mailing Services with a postage statement in order for monies to be available in LSU’s U.S. Postal Service account.
- Are you asking the vendor to deliver the job to Mailing Services for processing? If so, make sure Mailing Services is aware of the expected delivery.
- Regardless of how the job is mailed, it is good practice for Mailing Services to review a sample of the job before it is processed, to ensure it meets all USPS regulations. Please send a PDF to lsumailsvc@lsu.edu.
- To make arrangements with Mailing Services about these or other processes, please email lsumailsvc@lsu.edu.
Please refer to this chart to help you determine the process to mail your job:
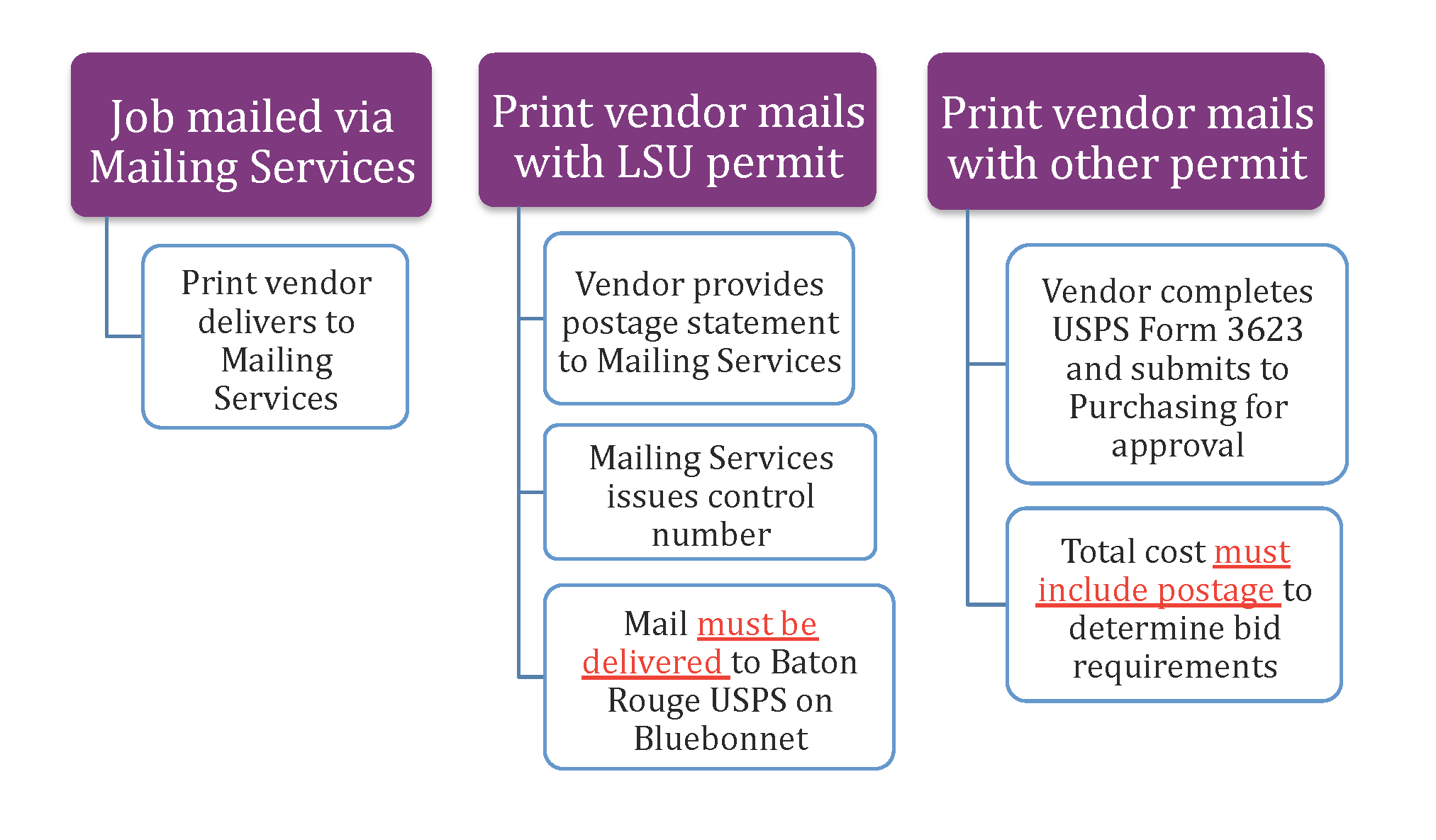
Billing: Departments may purchase printing under $5,000 without multiple quotes, and may pay via Procurement Card (if spending limits apply) or invoice. Projects costing more than $5,000 must be submitted to the Office of Purchasing as a requisition in PRO.
Please note: Purchasing will not approve charges over $5,000 “after the fact.” For example, if multiple alterations or other factors increased the initial price of a job to an amount over $5,000, then Purchasing will not approve the transaction.
Please see the chart below to determine vendor enrollment guidelines. When applicable, please direct vendors to enroll via online form.
Cost |
Purchase Order Required?
|
Vendor Enrollment Required? |
Method of Payment |
<$5,000 |
No |
No |
Procurement Card (spending limits apply) |
<$5,000 |
No |
Yes |
Invoice
|
>$5,000 |
Yes |
Yes |
Invoice |
For further guidance on purchasing printed materials, please contact Tiffany Carter (225-578-2739 Ext 8273 or email tcart12@lsu.edu).
Referenced from: lsu.edu